As urban populations swell, the demand for efficient warehousing within city limits is intensifying, Reuben Henry-Fellows reports…
As long as cities have existed, systems for storing and managing goods – urban warehouses – have existed to support and sustain these communities. Operating as the tangible nexus between global production and local consumption, between 1998 and 2004, urban warehouse square footage grew at an average of 2.5% per annum in the UK. The result is an industry now worth an estimated £36.3bn to the UK economy in 2024, vital to the sustainability of productive cities. However, as urban environments (which constitute 57% of the global population) continue to grow beyond the supportive capacity of their localities, the problems facing urban warehouses have increased proportionally. Thus, the modern urban warehouse industry has become mired in a complex and contesting web of logistic systems, each of which presents its own unique set of challenges.
Home is where the heart is
Urban warehouses gain greater efficacy the closer they are to the population they service. Reduced distribution times, operational costs and carbon emitted, in addition to easier access to potential workers and opportunities for quicker last mile solution options, all make placing a storage facility in the heart of a city incredibly profitable. Paradoxically however, the closer a warehouse is to the serviced area, the more problematic it becomes for residents due to increased congestion, air and noise pollution and increased demand (and therefore the price) of local property.
When considering new construction sites, warehouse operators are confined by their urban spatial context, facing negative externalities that inhibit their primary functions – a phenomenon known as Not in My Back Yard (NIMBY). While NIMBYism primarily affects the housing market, with a backlog of 4.3 million homes, it also significantly impacts the availability of new industrial and commercial construction sites. So pervasive is NIMBYism’s effect, that one of the first acts of the newly incumbent 2024 Labour government was chancellor Rachel Reeves’ speech reintroducing mandatory housing targets, announcing plans to reform the National Planning Policy Framework and relax existing planning laws.
Commenting on the difficulties of navigating land disputes when planning urban warehouses, director of fit out and refurbishment contractors, Pexhurst, Stuart Byles, says: “Nobody wants a delivery hub next to their home, or a school or playground, and there have been a few high-profile cases in the media in the past few years where communities have stopped larger fulfilment companies operating in their area.”
Additionally, once the site has been built, the regulatory guidelines consulted, and the delivery schedules have been created, retaining a highly skilled workforce becomes a challenge. A study by IFF research concluded that the turnover rate of warehouse workers is 37%, with the average job turnover rate at only 3.6%.
“Nobody wants a delivery hub next to their home, or a school or playground, and there have been a few high-profile cases in the media in the past few years where communities have stopped larger fulfilment companies operating in their area.” – Stuart Byles, director, Pexhurst
Despite the detractors, the rise of e-commerce, an industry worth £4.91tn by Forbes, has both cemented and magnified the benefits of urban warehousing, with an average annual market growth rate of 8%. This creates a positive feedback loop whereby increased growth promotes increased dependency, fostering further growth. To future-proof itself against increased demand in contention with limited and increasingly expensive space, the industry must find ways to better integrate into the cities of the future.
Mind of the machine
In 1994, pioneering the ‘smart city’ concept, the city of Amsterdam established a De Digital Stad (DDS) – or The Digital City. DDS was designed to provide residents with easy access to the internet, improving communication between themselves and their local government. At the advent of the 21st century, as the internet turned from novelty into societal ubiquity, the term ‘smart city’ evolved, becoming synonymous with urban environments that rely on internet and robotic systems to automate repetitive functions to the end of redeploying human labour to more value-added tasks.
Emulating this evolution, Amsterdam launched the ‘Amsterdam Smart City’ in 2009. Using DDS as a blueprint, planners designed the smart city around a holistic quadruple helix concept, integrating government, businesses, universities and research institutions and its citizens into planning and decision making. The project, which consists of 70 partners, including CISCO and IBM, indirectly led to an urban warehouse rent decrease (of properties over 5,000ft2) from €85 (£72) per square meter in 2014 to €65 (£55) per square meter in 2020, falling below Rotterdam (according to Statista). For comparison, Amsterdam’s rental market (which does not undergo the same regulatory standards) has risen to be the most expensive in continental Europe, averaging at €2,300 (£2,000) per month.
In the UK, where smart city initiatives have largely been confined to transport projects such as London’s Oyster or Manchester’s Bee Network, urban warehousing acts as a microcosm of the modern smart city – the smart warehouse. Through utilising interconnected and intelligent sites supported by data analytics and information and communication technology systems, smart warehousing in the UK can utilise technology to garner greater efficiency from smaller spaces.
With every inch a valuable, exploitable commodity, space retention and the commercialisation and modernisation of that space is imperative for urban warehouses to achieve maximum efficiency. Micro fulfilment centres or ‘micro-warehousing’ facilitate the immediacy of e-commerce deliveries, combining automated warehouse systems (AWS), greater space utilisation and capacity granularity – the minimum storage capacity acquired within a dataset.
“When space is limited, inventory optimisation becomes a finer art,” Byles continues. “You need leaders who have diverse experience and lateral thinking skills, thinking about stuff like seasonal demand fluctuations, and varying storage density based on the characteristics of different SKUs.”
However, with real-estate agent Knight Frank estimating approximately 60% – or 37.5m2 – of all warehouse space in units above 4,645ft2 in the UK failing to meet minimum EPC ‘B’ requirements by 2030, most of the country’s current warehousing will be rendered unlettable. Similarly, research conducted by CBRE Investment Management in 2023 indicates that even in Amsterdam (and Schiphol) approximately 43% of industrial stock is already obsolete. To combat this, many urban warehouses currently utilise common AWS including automated storage and retrieval systems (ASRS) automated picking systems, automated sortation systems and guided vehicles. Such systems utilise effective but decades old technology, the first ASRS developed in the 1950s, created for larger, less intensive work environments. As human labour costs continue to rise, companies are ensuring that their storage facilities are future proofed by employing more sophisticated robotic workers.
“Micro hubs enable real-time stock monitoring,” commercial director at blocz.io, Brian Boyer adds. “Drones with cameras are often used for this purpose. The video feed is ‘IT intensive’ in that it takes computing power and time to process the video. Reducing the processing time and improving the screen resolution improves accuracy but needs computing power that is nearer the warehouse.”
Drones equipped with machine-vision capabilities can be used to programme sortation cobots (collaborative robots) to conduct groundwork. Capable of moving independently along pre-planned routes, cobots can be fitted with sensory equipment such as RFID readers and barcode scanners to accelerate parcel picking bereft of human error. Additionally, cutting-edge robotic systems utilise machine learning AI to encode localised information concerning the robot’s routing i.e. consistent obstacles, pathing and efficient sortation methods, to improve efficiency.
FAST FACT: The warehousing and storage industry was estimated to be worth £37.1bn in 2023. Source: IBIS World
Studies conducted by global management consultant McKinsey concluded that AI-driven supply chains can cut costs by 15%, reduce inventory by 35%, and improve efficiency by 65%. Robotic warehouse systems equipped with machine learning can take this one step further, encoding adaptive systems that capable of independently selecting, sorting and storing products. Adopting AI models to improve on-demand warehousing is set to contribute to a surge in AI related business which is estimated to contribute to a 10.3% GDP increase – equivalent to £232bn – by 2030, according to accountancy firm PWC.
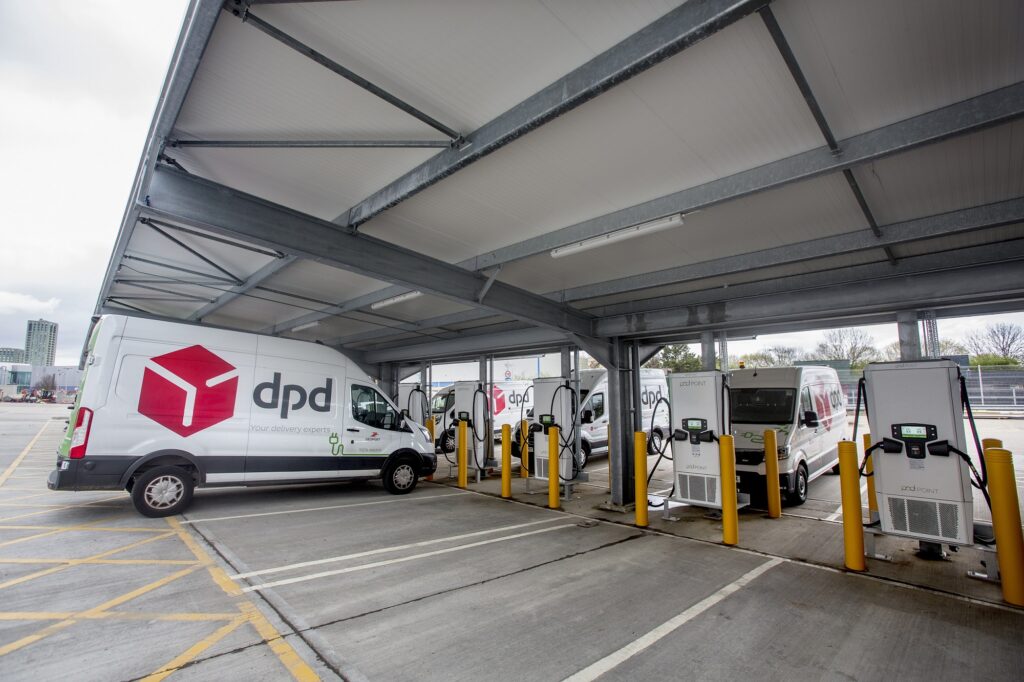
Detailing the advancements needed to integrate urban warehousing into smart cities, Boyer says: “It’s no longer enough to rely on conventional telecommunications networks – they need to start bringing computing power closer to the point of need, which means smaller, more energy efficient data centres.”
Practice makes perfect
For the largest delivery companies, mechanising last-mile logistics options remains one of the fastest and cost-effective methods of smart warehousing enhancement. However, small and midsize enterprises can only partially automate their operations due to cost restraints. Electrifying last-mile logistics, thereby adhering to tighter environmental and building regulations, therefore confers massive benefits.
Reducing fuel costs is so imperative to improving operational gains that when e-commerce giant Amazon opened its first micromobility hub in Belfast, Northern Ireland, it implemented the use of e-cargo bikes for last-mile delivery as a cornerstone of production. With freight transport constituting 30% of global road-based carbon emissions (reported by climate charity Possible), Amazon’s £300m investment to electrify and decarbonise Amazon’s UK transportation network could save 389kg of CO2 per 1,000 bikes per annum.
“Autonomous mobility will be a key lever for decarbonisation, as it transforms last-mile transportation into a much greener process. By partnering with delivery companies such as DPD we’re propelling this transformation forward, making sustainable delivery the norm, rather than a nice to have.” – Anjali Jindal Naik, co-founder and COO, Cartken
Discussing how last-logistics can support urban warehouses, James Watson, partner at Tritax, adds: “Various types of facilities can support last-mile logistics in urban areas. Traditionally, these have included urban fulfilment centres, micro fulfilment centres, and dark stores – though these are now in decline as retailers have leveraged their existing portfolios more effectively. Larger out-of-town retail assets are particularly well-suited to support last-mile, allowing retailers to pick and ship from their existing facilities to support e-commerce fulfilment.”
When international parcel delivery service DPD opened its flagship London sortation centre in Bromley-By-Bow, Docklands, the size of the operation similarly necessitated the facility’s planners ensure the most efficient, sustainable and cost-effective delivery possible. DPD opted for electric delivery vans, outfitting the site with capacity for 500 vehicles each of which is capable of 80,000 parcels into London delivers daily. To do so, DPD utilised previously derelict storage, improving the preexisting infrastructure without impacting the local community with new, potentially divisive building plans.
Tim Jones, director of marketing, communications and sustainability at DPD Group UK, says: “We have invested significantly to ensure that the building and the infrastructure, including the charging capacity, can be upgraded in future. We have also reimagined processes to make the operation smarter and more sustainable for example, being able to accommodate a series of delivery waves throughout the day and investing in a state-of-the-art conveyor system that automatically sorts all intra-London parcels for next-day delivery on-site.”
FAST FACT: Total UK warehousing space now covers 690,000ft2 reflecting a 22% increase in the last three years Source: IBIS World
DPD’s upgraded facility, which is the size of 8.5 football pitches, seeks to further reduce costs through the solar panels on the parking canopy to help charge the delivery vans and a 40,000 litre HVO tank to enable the fleet of LGVs and 7.5-tonne trucks to fill-up with the renewable biofuel. The company has already extensively trialled autonomous last-mile delivery robots, having launched 10 pilot schemes throughout southeast England in 2022. Each of the Cartken level 4 autonomous vehicles possesses micro-autonomous vehicle technology that enables full autonomy on footpaths with only machine vision operated cameras.
Speaking at the time of the launch in 2022, Cartken co-founder and COO Anjali Jindal Naik, said: “Autonomous mobility will be a key lever for decarbonisation, as it transforms last-mile transportation into a much greener process. By partnering with delivery companies such as DPD we’re propelling this transformation forward, making sustainable delivery the norm, rather than a nice thing to have.”
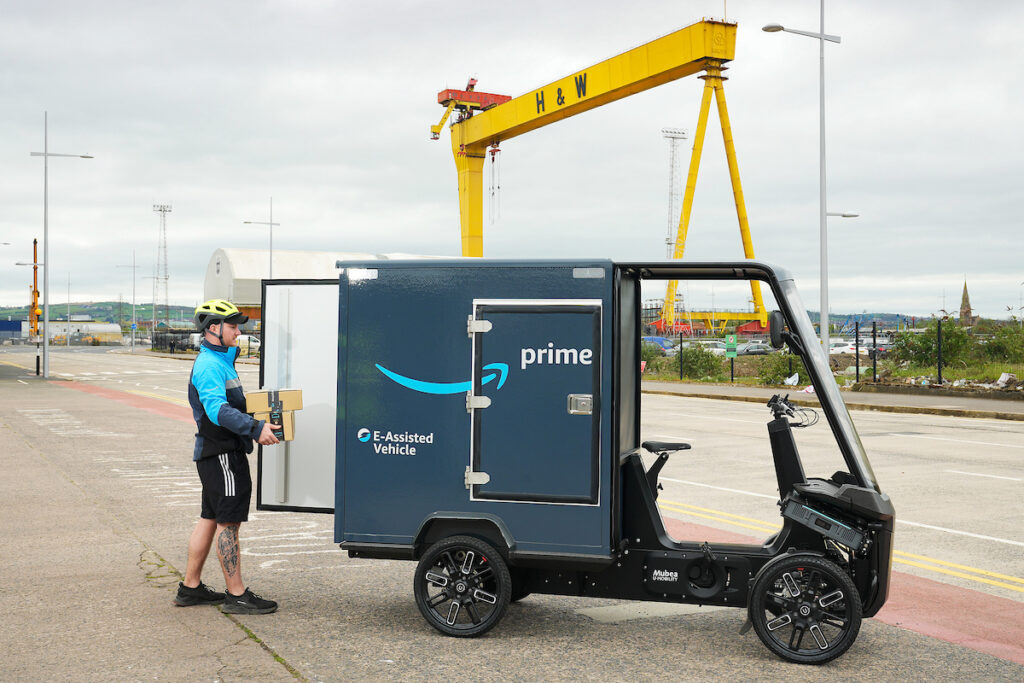
At DPD’s flagship London depot, the delivery company is focused on integrating its facilities into the surrounding with minimal friction, pioneering smart warehousing principles as key tenements of operational functions.
The multitude of contesting factors that affect urban warehouses hinge on what multifaceted approach the industry takes to future-proofing this critical component of modern cities. Each challenge presents an opportunity for smart warehousing which, if managed with innovative and adaptive strategies, is free of the spatial, regulatory, workforce and environmental issues of their traditional counterparts. However, advances in AWS, machine learning AI and environmental practices facilitate greater gains in operational efficiency. The traditional proximity of urban warehouses, once a fault of their design, can be utilised as the crucible through which industry reform can be achieved.
This article was originally published in the September 2024 issue of CiTTi Magazine.
Achievements and innovations in urban logistics will be celebrated at the third annual CiTTi Awards, which will be held on 26 November 2024 at De Vere Grand Connaught Rooms in London. Please visit www.cittiawards.co.uk to learn more about this unmissable event for the UK’s transportation sector – and to book your table!